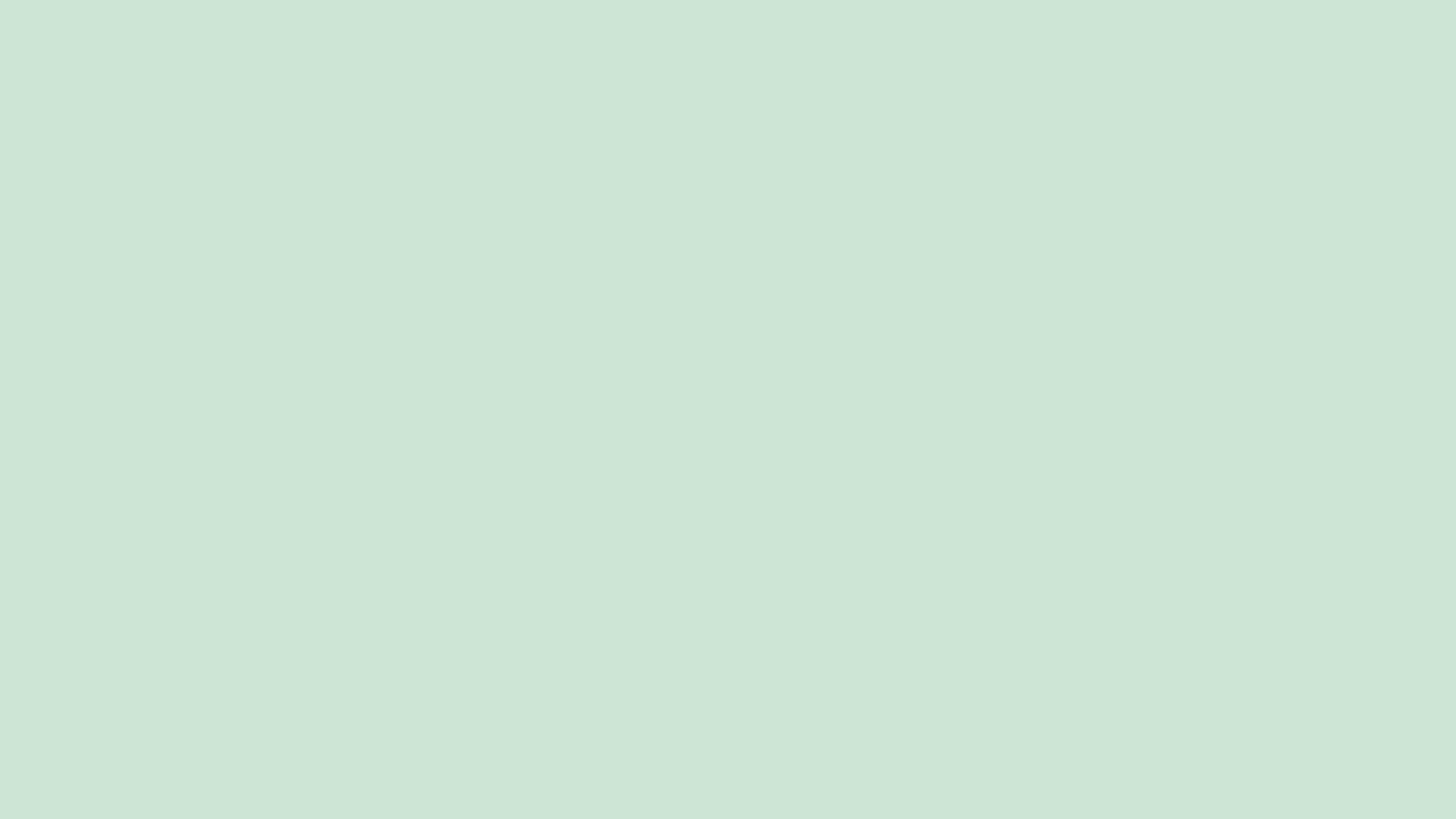
E112
17.09.2010
Patent E112 - IP Portfolio A1
Spring-Decoupled Electrohydraulic Follow-Up Brake Booster
Inventors: H. Leiber, Dr. T. Leiber, V. Unterfrauner
3 Core Innovations
Patent E112DE
Spring-Decoupled Electrohydraulic Follow-Up Brake Booster
Patent Status : Upheld
Patent E112DE1
Adaptive Stroke Differential Position Control For Brake Boosting
Patent Status : Revoked
Appeal Pending
Patent E112DE2
Electrohydraulic Follow-up Brake Booster Including Brake Boost and Basic ABS
Patent Status : Revoked
Appeal Pending
Patent E112DE (DE112009004636B4)
Keyword: Spring-Decoupled Electrohydraulic Follow-Up Brake Booster
Upheld by the Federal Supreme Court – valid through 2029.
1.Brake system,
2.an electric motor brake booster with an electric motor (11, 12) for driving a master brake cylinder or tandem master brake cylinder (5),
3.wherein the working chamber or chambers of the brake booster are connected via hydraulic lines (6, 7) to the wheel cylinders of wheel brakes (9a-9d)
4.and a controllable valve (8a, 8b, 8c, 8d) is assigned to each wheel brake (9a-9d),
5.and that a control device causes pressure to be built up and released in the wheel brakes (9a-9d) simultaneously or successively by means of the brake booster and the controlled valves (8a-8d),
characterized in that
6.a brake actuation device (16, 16a, 14), comprising a brake pedal (16) and a transmission device (14),
7.acts in a force-assisted manner on the piston (24) of the brake booster during normal braking operation,
8.wherein the brake actuating device (16, 16a, 14) acts on the piston (24) of the brake booster via at least one spring element (20, 20b),
9.wherein the brake system has sensors (4, 22) for determining the piston position and the position of the brake actuating device (16, 16a, 14),
10.wherein the sensors (4, 22) are arranged to detect a possible difference in travel between the piston (24) and the brake actuating device (16, 16a, 14) due to the spring element (20, 20b),
11.and the control device of the brake system controls the drive of the brake booster depending on the difference in travel,
12.wherein, when the brake pedal (16) is not actuated, a spring (17) lifts the transmission device (14) away from the piston (24) by a dead stroke Δs.
Claim Features
Abstract:
The innovation describes an electrohydraulic fail-safe brake-by-wire (F-BbW) braking system in which a driver-operated brake pedal is decoupled from the piston of the electric motor-driven brake booster by an elastic element; sensors measure the difference in travel between the pedal and piston positions, and the control unit uses this difference to actuate the electric motor in a demand- and force-assisted manner, while a defined idle stroke lifts the pedal off the piston when at rest.
Technical Relevance:
The claim precisely captures the principle of the electro-hydraulic regenerative brake booster (springs with defined idle stroke + travel difference sensor + motor control based on differential travel control) and the valve-based wheel individualization that modern electro-hydraulic follow-up brake boosters use to provide fast pressure dynamics, recuperation blending and fail-safe capability without a vacuum pump.
Patent E112DE1 (DE112009005536B3)
Keyword: Adaptive Stroke Differential Position Control For Electromechanical Brake Boosting
Method for controlling electromechanical brake boosting, in which the master brake cylinder or tandem master brake cylinder (5) is driven by an electric motor (11, 12),
wherein a brake actuating device (16, 16a, 14) acts in a force-assisting manner on a spindle (13) and/or a piston (24) of the brake booster during normal braking operation, comprising the steps of
Detecting a piston travel (sK) of the master brake cylinder or tandem master brake cylinder (5), where- wherein the piston travel (sK) is detected via a rotation angle sensor (4) of the electric motor (11, 12);
Detection of a stroke of the brake actuating device (16, 16a, 14);
Determining a path difference (Δh) between the piston (24) and the brake actuating device (16, 16a, 14), based on the detected piston path (sK) and the detected stroke of the brake actuating device (16, 16a, 14)
Using the path difference (Δh) to control the electromotive brake force amplification.
Claim Features
Abstract:
The invention relates to a method for controlling an electromotive brake booster, in which the path difference between the piston of the master brake cylinder and the brake actuating device is determined by means of a rotation angle sensor and a pedal stroke sensor and is used for precise control of the force-assisting motor actuation.
Technical Relevance:
The technical relevance of this invention lies in its central importance for modern brake-by-wire and electromechanical follow-up brake booster systems, in particular as a preliminary stage or component of so-called e-booster concepts.
This invention represents an intelligent control approach for electromechanically assisted brake systems and forms an essential basis for modern e-booster architectures.
Patent E112DE2 (DE11 2009 005 541)
Keyword: Electrohydraulic Follow-up Brake Booster Including Brake Boost and Basic ABS
Claim Features
Brake system, comprising an electromotive brake booster, in which the master brake cylinder or tandem master brake cylinder (5) is driven by an electric motor (11, 12) via a spindle drive with a spindle (13),
wherein the working chamber or chambers of the brake booster are connected via hydraulic lines (6, 7) to the wheel cylinders of wheel brakes (9a-9d)
and a controllable valve (8a-8d) is assigned to each wheel brake (9a-9d), and in that pressure build-up and pressure reduction in the wheel brakes (9a-9d) by means of the brake booster and the controlled valves (8a-8d) take place simultaneously or successively by means of a control device,
characterized in that a brake actuating device (16, 16a, 14) acts in a force-assisting manner on a piston (24) of the brake booster during normal braking operation, the spindle (13) or the piston (24) applying force to and/or adjusting the brake actuating device (16, 16a, 14) during ABS operation
and the piston (24) of the brake booster is moved back and forth via the electric motor (11, 12) to adjust the wheel brake pressures.
Abstract:
The invention describes an electrohydraulic fail-safe brake-by-wire (F-BbW) brake system with an electric motor spindle drive, in which a piston in the master brake cylinder builds up or reduces the pressure in the wheel brakes via selectively controlled valves, whereby in normal operation the pedal force is supported and in ABS operation the electric motor actively moves the piston for pressure regulation and also acts retroactively on the pedal device.
Technical Relevance:
TThe technical relevance of this invention lies in its central importance for electromechanical progressive brake booster systems, in particular as a preliminary stage or component of so-called e-booster concepts. This invention provides an intelligent control approach for the simple integration of a brake booster and an ABS function with a very simple, low-cost path simulator with driver request detection via differential path detection.