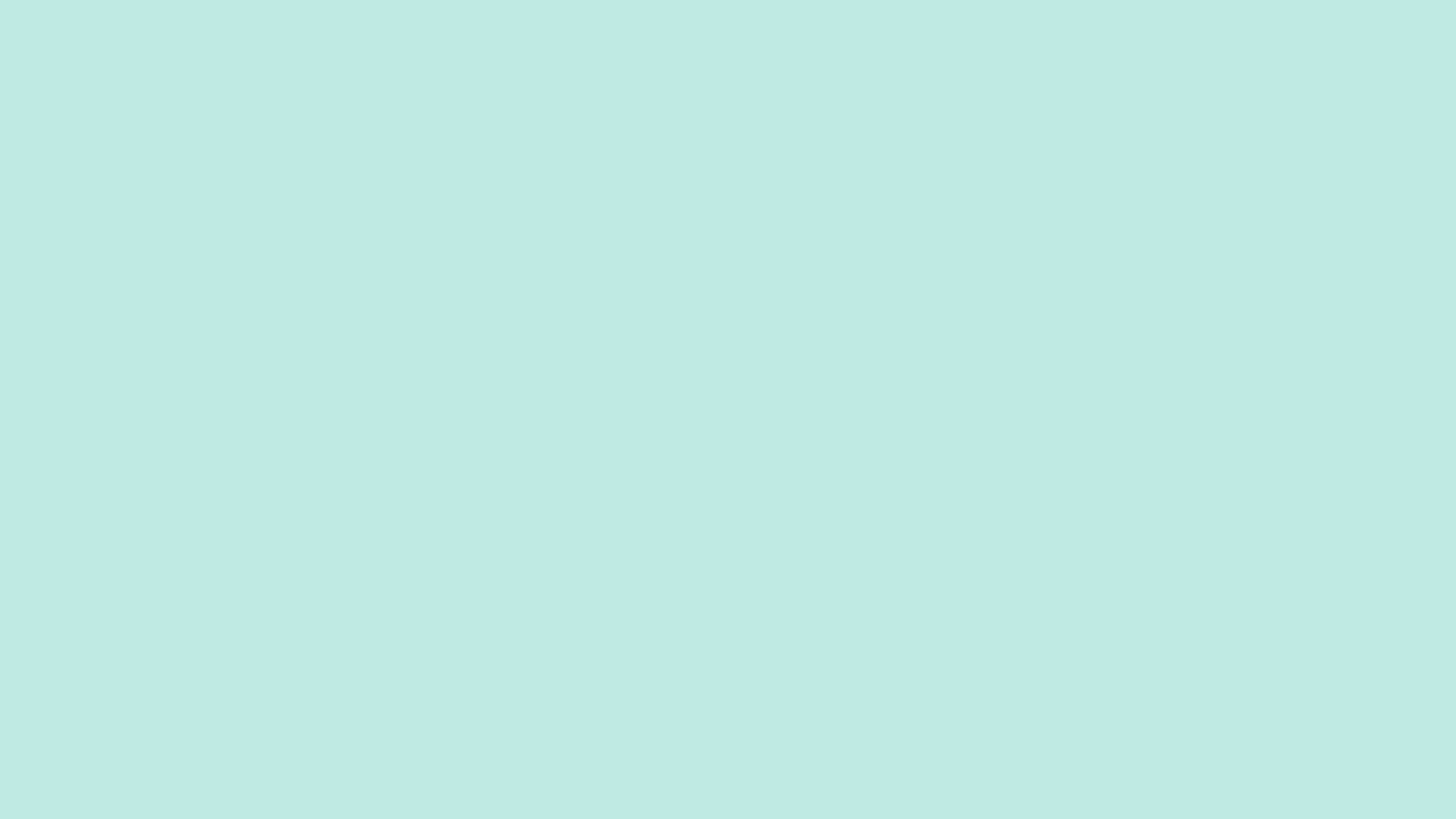
E102
13.2.2009
Patent E102 - IP Portfolio A2
HDC Control in Two Parts; Plunger Flow Control and Valve Modulation.
Inventors: Inventors: H. Leiber, C. Köglserperger, Dr. A. van Zanten
20 Core Innovations
Patent E102EP
Plunger Flow Control - adaptive pressure gradient regulation via piston dynamics
1 claim
Patent Status : Granted
Patent E102DE
Brake pressure distribution with Plunger Flow Control and PWM-controlled 2/2-way valves
1 claim
Patent Status : Granted
Patent E102DE1
Plunger flow control with wheel-selective valve control
4 claims
Patent Status : Granted
Patent E102DE2
Plunger flow control with pressure curve control
5 claims
Patent Status : Granted
Patent E102DE3
Plunger & Valve-Sync - simultaneous pressure control with wheel-selective PWM valve control
3 claims
Patent Status : Examining
Patent E102DE4
Plunger Flow Control with model-based pressure curve estimation
5 claims
Patent Status : Examining
Patent E102EP (EP 2396202)
Keyword: Plunger Flow Control - Adaptive Pressure Gradient Regulation via Piston Dynamics
Brake system with a brake booster, the piston-cylinder system (14, HZ, THZ) of which is driven mechanically or hydraulically by an electric motor, in particular by transmission means,
wherein at least one working chamber of the piston-cylinder system (14, HZ, THZ) is connected via hydraulic lines to at least two wheel brakes,
wherein a 2/2-way switching valve (17a, 17b, 17c, 17d) is assigned to each wheel brake and the hydraulic connecting lines between the wheel brakes (18a, 18b, 18c, 18d) and the piston-cylinder system (14, HZ, THZ) can be closed either separately or jointly by means of the 2/2-way switching valves (17a, 17b, 17c, 17d), so that the hydraulic lines between the wheel brakes (18a, 18b, 18c, 18d) and the piston-cylinder system (14, HZ, THZ) can be closed either separately or jointly. so that a pressure can be regulated in the wheel brakes (18a, 18b, 18c, 18d) successively in the sense of a multiplex process and/or simultaneously,
the electric motor and the switching valves (17a, 17b, 17c, 17d) being controlled by a control device, and in that the hydraulic connecting line from the working chamber of the piston-cylinder system (14, HZ, THZ) to the respective switching valve designed as a solenoid valve has a flow resistance (RLi ) and each switching valve together with the hydraulic line to the wheel cylinder (17a, 17b, 17c, 17d) has a flow resistance (RV),
characterized in that the flow resistances (RLi ) and (RVi ) are small, such that the piston speed of the piston of the piston-cylinder system (14, HZ, THZ) determines the pressure reduction gradient and pressure build-up gradient in each wheel brake (18a, 18b, 18c, 18d),
wherein the flow resistance (RLi ) is smaller than the flow resistance (RVi ), and in that the control device regulates or controls the piston movement and piston speed during pressure build-up and pressure reduction as a function of the pressure-volume characteristic of the wheel brakes (18a, 18b, 18c, 18d),
and in that the flow resistances (RLi ) and (RVi ), in particular the sum of the flow resistances (RLi ) and (RVi ) of each wheel brake (18a, 18b, 18c, 16d), are or are designed in such a way that with maximum dynamics of the piston-cylinder system (HZ) and its drive and at least two or more open switching valves (17a, 17b, 17c, 17d), no pressure equalization takes place between the wheel brakes (18a, 18b, 18c, 18d) due to the simultaneous volume intake or volume release of the wheel brakes (18a, 18b, 18c, 18d) during the time in which the switching valves (17a, 17b, 17c, 17d) are open.
Claim Features
Abstract:
The central idea of the invention consists in an electrically driven brake-by-wire (BbW) brake system which enables highly dynamic and precise pressure control by means of a flow-optimized hydraulic design with low pressure losses. During pressure build-up and reduction, the piston (plunger) is advanced and retracted in a definite manner. The pressure is controlled via a combined control of the piston position and speed, taking into account the pressure-volume characteristic of the brake system. This type of control is referred to as plunger flow control in the following.
Technical Relevance:
The aim of the invention is to precisely control not only the target pressure, but also the time profile of the brake pressure - in particular the gradients during pressure build-up and reduction. This is achieved by closed-loop control of the piston movement, taking into account the specific pressure-volume characteristic.
Although initially intended for use in classic ABS operation, the technology has become particularly popular in the context of recuperative braking processes with blending. Here, the sensitive and low-noise pressure modulation enables dynamic adaptation to the variable generator torque - a prerequisite for efficient and comfortable blending. Compared to conventional outlet valves, plunger control offers considerable advantages: it avoids typical switching noises and eliminates the inaccuracies of time-controlled pressure reduction processes caused by valve switching times.
This is implemented using a cascaded control architecture:
- The inner, fast control loop controls the piston position and speed highly dynamically.
- The outer, slower control loop provides the higher-level control of the desired brake pressure.
This control structure is used in particular in modern one-box brake systems from leading manufacturers - for example, in 2- or 4-wheel blending systems and in electronic brake force distribution (EBD), especially with simultaneous recuperation.
Patent E102DE (DE102009008944)
CLAIM 1
Keyword: Brake Pressure Distribution With Plunger Flow Control And Pwm-controlled 2/2-way Valves
Brake system with a brake booster, the piston-cylinder system (14) of which is driven mechanically or hydraulically by transmission means from an electric motor, at least one working chamber of the piston-cylinder system (14) being connected via hydraulic lines to at least two wheel brakes (18a, 18b, 18c, 18d),
wherein a 2/2-way switching valve (17a, 17b, 17c, 17d) is assigned to each wheel brake and the hydraulic connecting lines between the wheel brakes (18a, 18b, 18c, 18d) and the piston-cylinder system (14) are connected either separately or jointly by means of the 2/2-way switching valves (17a, 17b, 17c, 17d), so that a pressure can be regulated in the wheel brakes (18a, 18b, 18c, 18d) successively in the sense of a multiplex process and/or simultaneously,
wherein the electric motor and the switching valves (17a, 17b, 17c, 17d) are controlled by a control device, and that the hydraulic connecting line from the working chamber of the piston-cylinder system (14) to the respective solenoid valve has a flow resistance RLi and each switching valve together with the hydraulic line to the wheel cylinder has a flow resistance RVi,
wherein the flow resistances RLi and RVi are small such that the HZ piston speed determines the pressure reduction gradient and pressure build-up gradient in each wheel brake (18a, 18b, 18c, 18d),
wherein the flow resistance RLi is smaller than the flow resistance RVi,
characterized in that, in the event of simultaneous or partially simultaneous pressure build-up or pressure reduction in the at least two wheel brakes (18a, 18b, 18c, 18d), the control device controls at least one of the switching valves (17a, 17b, 17c, 17d) assigned to the at least two wheel brakes (18a, 18b, 18c, 18d) by means of pulse width modulation in such a way that the flow resistance of this at least one switching valve (17a, 17b, 17c, 17d) is increased.
Claim Features
Abstract:
The patent describes an electrohydraulic brake-by-wire (BbW) brake system with a piston-cylinder system driven by an electric motor, which supplies several wheel brakes individually or simultaneously with brake pressure via 2/2-way switching valves using a multiplex process, whereby the flow resistance of individual valves is adapted by definite pulse width modulation in order to enable precise pressure build-up or reduction per wheel brake.
Technical Relevance:
The primary technical relevance of the invention lies in the selective, wheel-specific pressure control, which is particularly important for driving dynamics interventions and for the combination with regenerative braking. For example, during a braking process with simultaneous steering intervention, the brake pressure build-up on certain wheels can be controlled directly via plunger flow control, while on other wheels the pressure is built up via individual pulse width modulation (PWM). This wheel-selective control enables precise coordination between driving stability and energy efficiency - especially in complex driving conditions.
Patent E102DE1 (DE 102009061889)
CLAIM 1
Keyword: Plunger Flow Control With Wheel-Selective Valve Control
Claim Features
Brake system with a brake booster whose piston-cylinder system (14, HZ, THZ) is mechanically or hydraulically driven by an electric motor by transmission means,
wherein at least one working chamber of the piston-cylinder system (14, HZ, THZ) is connected via hydraulic lines to at least two wheel brakes (18a, 18b, 18c, 18d), the wheel brakes (18a, 18b, 18c, 18d) each being assigned a 2/2-way switching valve (17a, 17b, 17c, 17d), 17c, 17d) is assigned to each of the wheel brakes (18a, 18b, 18c, 18d) and the hydraulic connecting lines between the wheel brakes (18a, 18b, 18c, 18d) and the piston-cylinder system (14, HZ) can be closed either separately or jointly by means of the 2/2-way switching valves (17a, 17b, 17c, 17d),
so that a pressure can be set in the wheel brakes (18a, 18b, 18c, 18d) simultaneously or overlapping in time,
wherein the electric motor can be controlled by a control device in such a way that in a pressure reduction phase a (main) cylinder pressure (pHZ) generated by means of the piston-cylinder system (14) is changed over time,
wherein the 2/2-way switching valves (17a, 17b, 17c, 17d) can be controlled by the control device in the pressure reduction phase in such a way
that at least in one time interval at least one first 2/2-way switching valve (17a, 17b, 17c, 17d) is open and at least one second 2/2-way switching valve (17a, 17b, 17c, 17d) is controlled by means of pulse width modulation such that the flow resistance of the second 2/2-way
switching valve (17a, 17b, 17c, 17d) is increased, and/or that at least one first 2/2-way switching valve (17a, 17b, 17c, 17d) is closed and at least one second 2/2-way switching valve (17a, 17b, 17c, 17d) is opened at least in one time interval.
Abstract:
The patent protects an electro-hydraulic brake-by-wire (BbW) braking system in which a brake booster driven by an electric motor generates the master cylinder pressure, which is distributed wheel-selectively to at least two wheel brakes by means of 2/2-way valves (open, closed, PWM-controlled) which are controlled individually or overlapping in time, so that highly dynamic and precise brake pressures can be set during pressure reduction.
Technical Relevance:
The brake system couples a highly dynamically controlled piston actuator with 2/2 valves, which are opened, closed or throttled via PWM as required. The PWM control can prevent brake fluid from flowing directly from one wheel brake cylinder with the high pressure into the wheel brake cylinder with the lower pressure during simultaneous pressure reduction and the pressure in the wheel brake cylinder with the lower pressure being built up instead of being reduced. With such simultaneous pressure reduction, friction brake interventions can be mixed in milliseconds for individual axles or wheels during recuperation processes, as well as precise driving dynamics interventions - ideal for electric vehicles with several electric drive motors on the front and rear axles and for torque vectoring interventions.
Patent E102DE1 (DE 102009061889)
CLAIM 2
Keyword: Plunger Flow Control With Wheel-Selective Valve Control
Claim Features
Brake system with a brake booster whose piston-cylinder system (14, HZ, THZ) is mechanically or hydraulically driven by an electric motor by transmission means,
wherein at least one working chamber of the piston-cylinder system (14, HZ, THZ) is connected via hydraulic lines to at least two wheel brakes (18a, 18b, 18c, 18d), the wheel brakes (18a, 18b, 18c, 18d) each being assigned a 2/2-way switching valve (17a, 17b, 17c, 17d), 17c, 17d) is assigned to each of the wheel brakes (18a, 18b, 18c, 18d) and the hydraulic connecting lines between the wheel brakes (18a, 18b, 18c, 18d) and the piston-cylinder system (14, HZ) can be closed either separately or jointly by means of the 2/2-way switching valves (17a, 17b, 17c, 17d),
so that a pressure can be set in the wheel brakes (18a, 18b, 18c, 18d) simultaneously or overlapping in time,
wherein the electric motor can be controlled by a control device in such a way that in a pressure build-up phase a (main) cylinder pressure (pHZ) generated by means of the piston-cylinder system (14) is changed over time,
wherein the 2/2-way switching valves (17a, 17b, 17c, 17d) can be controlled by the control device in the pressure build-up phase in such a way
that at least in one time interval at least one first 2/2-way switching valve (17a, 17b, 17c, 17d) is open and at least one second 2/2-way switching valve (17a, 17b, 17c, 17d) is controlled by means of pulse width modulation such that the flow resistance of the second 2/2-way switching valve (17a, 17b, 17c, 17d) is increased,
and/or that at least one first 2/2-way switching valve (17a, 17b, 17c, 17d) is closed and at least one second 2/2-way switching valve (17a, 17b, 17c, 17d) is opened at least in one time interval.
Abstract:
The patent protects an electro-hydraulic brake-by-wire (BbW) braking system in which a brake booster driven by an electric motor generates the master cylinder pressure, which is distributed wheel-selectively to at least two wheel brakes by means of 2/2-way valves (open, closed, PWM-controlled) which are controlled individually or overlapping in time, so that highly dynamic and precise brake pressures can be set during the pressure build-up.
Technical Relevance:
The brake system couples a highly dynamically controlled piston actuator with 2/2 valves, which can be opened, closed or throttled via PWM as required, so that during pressure build-up, brake torque interventions can be mixed in milliseconds for individual axles or wheels during recuperation processes, as well as precise driving dynamics interventions - ideal for electric vehicles with several electric drive motors on the front and rear axles and for torque vectoring interventions.
Patent E102DE1 (DE 102009061889)
CLAIM 18
Keyword: Plunger Flow Control With Wheel-Selective Valve Control
Claim Features
Brake system with a brake booster whose piston-cylinder system (14, HZ, THZ) is mechanically or hydraulically driven by an electric motor via transmission means,
wherein at least one working chamber of the piston-cylinder system (14, HZ, THZ) is connected via hydraulic lines to at least two wheel brakes (18a, 18b, 18c, 18d), the wheel brakes (18a, 18b, 18c, 18d) each being assigned a 2/2-way switching valve (17a, 17b, 17c, 17d), 17c, 17d) is assigned to each of the wheel brakes (18a, 18b, 18c, 18d) and the hydraulic connecting lines between the wheel brakes (18a, 18b, 18c, 18d) and the piston-cylinder system (14, HZ) can be closed either separately or jointly by means of the 2/2-way switching valves (17a, 17b, 17c, 17d),
so that a pressure can be set in the wheel brakes (18a, 18b, 18c, 18d) simultaneously or overlapping in time,
wherein the electric motor can be controlled by a control device in such a way that in a pressure reduction phase a (main) cylinder pressure (pHZ) generated by means of the piston-cylinder system (14) is changed over time,
wherein the 2/2-way switching valves (17a, 17b, 17c, 17d) can be controlled by the control device in the pressure reduction phase in such a way
that at least in one time interval at least one first 2/2-way switching valve (17a, 17b, 17c, 17d) is open and at least one second 2/2-way switching valve (17a, 17b, 17c, 17d) is controlled by means of pulse width modulation such that the flow resistance of the second 2/2-way switching valve (17a, 17b, 17c, 17d) is increased,
and/or that at least one first 2/2-way switching valve (17a, 17b, 17c, 17d) is closed and at least one second 2/2-way switching valve (17a, 17b, 17c, 17d) is opened at least in one time interval
Abstract:
The patent protects a method for high-precision pressure adjustment for the pressure reduction of an electro-hydraulic brake-by-wire (BbW) brake system, in which a brake booster driven by the electric motor generates the master cylinder pressure, which is distributed wheel-selectively by means of 2/2-way valves (open, closed, PWM-controlled) controlled individually or overlapping in time, so that highly dynamic and precise brake pressures can be set during pressure reduction.
Technical relevance:
The method for adjusting the pressure of a brake system couples a highly dynamically controlled piston actuator with 2/2 valves, which are opened, closed or throttled via PWM as required, so that during pressure reduction, friction brake interventions can be mixed in milliseconds for each axle or wheel individually during recuperation processes, as well as precise driving dynamics interventions - ideal for electric vehicles with several electric drive motors on the front axle and rear axle as well as for torque vectoring interventions
Patent E102DE1 (DE 102009061889)
CLAIM 19
Keyword: Plunger Flow Control With Wheel-Selective Valve Control
Claim Features
Method for adjusting a brake pressure using a brake system according to claim 2,
characterized in that the pressure is built up in at least two wheel brakes (18a, 18b, 18c, 18d) simultaneously or overlapping in time,
wherein the electric motor is controlled by a control device in such a way that a (master) cylinder pressure (pHZ) generated by means of the piston-cylinder system (14) is changed over time, wherein the 2/2-way switching valves (17a, 17b, 17c, 17d) are controlled by the control device in such a way,
that at least in one time interval at least one first 2/2-way switching valve (17a, 17b, 17c, 17d) is open and at least one second 2/2-way switching valve (17a, 17b, 17c, 17d) is controlled by means of pulse width modulation in such a way,
that the flow resistance of the second 2/2-way switching valve (17a, 17b, 17c, 17d) is increased,
and/or that at least one first 2/2-way switching valve (17a, 17b, 17c, 17d) is closed and at least one second 2/2-way switching valve (17a, 17b, 17c, 17d) is opened at least in one time interval
Abstract:
The patent protects a method for high-precision pressure adjustment for the pressure build-up of an electro-hydraulic brake-by-wire (BbW) brake system, in which a piston driven by the electric motor generates the master cylinder pressure, which is distributed wheel-selectively by means of 2/2-way valves (open, closed, PWM-controlled) controlled individually or overlapping in time, so that highly dynamic and precise brake pressures can be set during the pressure build-up.
Technical Relevance:
The method for adjusting the pressure of a brake system couples a highly dynamically controlled piston actuator with 2/2 valves, which are opened, closed or throttled via PWM as required, so that during pressure build-up, friction brake torque component interventions can be mixed in milliseconds on an axle- or wheel-specific basis during recuperation processes, as well as precise driving dynamics interventions - ideal for electric vehicles with several electric drive motors on the front axle and rear axle, as well as for torque vectoring interventions.
Patent E102DE2 (DE 102009061892)
CLAIM 1
Keyword: Plunger Flow Control with pressure curve control and pressure balancing
Method for adjusting a brake pressure in a brake system with four wheel brakes (18a, 18b, 18c, 18d) using a piston-cylinder system (14, HZ, THZ),
wherein a solenoid valve (17a, 17b, 17c, 17d) is associated with each of the wheel brakes (18a, 18b, 18c, 18d), The method comprising the following steps:
performing a pressure build-up in at least one selected wheel brake (18a, 18b, 18c, 18d) when a pressure change in the selected wheel brake (18a, 18b, 18c, 18d) is required,
wherein the pressure build-up in the selected wheel brake (18a, 18b, 18c, 18d) comprises the following steps:
displacement of a piston of the piston-cylinder system (14, HZ, THZ) by the electric motor, so that in a pressure build-up phase a pressure (pR1, pR2) is built up at least in the selected wheel brake (18a, 18b, 18c, 18d) in such a way that in
a first time interval of the pressure build-up phase, a difference between a pressure (pHZ) in the piston-cylinder system (14, HZ, THZ) and the pressure (pR1, pR2) in the selected wheel brake (18a, 18b, 18c, 18d) increases
and in a second time interval of the pressure build-up phase, the difference between the pressure (pHZ) in the piston-cylinder system (14, HZ, THZ) and the pressure (PR1, PR2) in the selected wheel brake (18a, 18b, 18c, 18d) decreases.
Claim Features
Abstract:
The patent describes a method for wheel-selective pressure control, in which an electrically driven master piston in a first phase selectively builds up a pressure difference between the master brake cylinder and one or more selected wheel brake cylinders during pressure build-up. In a second phase, this difference is balanced out again in a controlled manner so that the brake pressure in the respective wheels is generated quickly, precisely and almost silently.
Technical Relevance:
The two-phase pressure build-up enables highly dynamic and at the same time low-noise brake pressure interventions within milliseconds - wheel-specific, efficient and sensitive. At the end of the second phase, pressure equalization takes place between the master brake cylinder and the wheel brake cylinder. The pressure sensor in the pressure supply (piston cylinder system) then also displays the pressure in the wheel brake cylinder. This allows the volume-pressure curve of the wheel brake cylinder to be adapted after each completed pressure change. In addition, the required target position change of the piston-cylinder system for the final target pressure to be set in the selected wheel brake(s) is calculated by knowing the volume-pressure curve of the individual wheel brakes. The process enables precise control of the brake pressures at the individual wheels without the need for expensive wheel pressure sensors. Instead, a central pressure sensor is sufficient, which ideally records the output pressure of the electric motor-driven pressure generation unit directly. This is particularly advantageous for modern, software-defined driving dynamics functions such as torque vectoring or recuperation braking in electric vehicles, where precision, comfort and energy efficiency have top priority.
Patent E102DE2 (DE 102009061892)
CLAIM 2
Keyword: Plunger Flow Control with pressure curve control and pressure balancing
Claim Features
Method for adjusting a brake pressure in a brake system with four wheel brakes (18a, 18b, 18c, 18d) using a piston-cylinder system (14, HZ, THZ),
wherein a solenoid valve (17a, 17b, 17c, 17d) is associated with each of the wheel brakes (18a, 18b, 18c, 18d),
wherein the method comprises the following step
carrying out a pressure build-up in at least one selected wheel brake (18a, 18b, 18c, 18d) when a pressure change in the selected wheel brake (18a, 18b, 18c, 18d) is required,
wherein the pressure build-up in the selected wheel brake (18a, 18b, 18c, 18d) comprises the following steps: displacement of a piston of the piston-cylinder system (14, HZ, THZ) by the electric motor, so that in a pressure build-up phase a pressure (pR1, pR2 ) is built up at least in the selected wheel brake (18a, 18b, 18c, 18d) in such a way,
that in a first time interval of the pressure build-up phase, a difference between a pressure (pHZ ) in the piston-cylinder system (14, HZ, THZ)
and the pressure (pR1 , pR2 ) in the selected wheel brake (18a, 18b, 18c, 18d) increases
and in a second time interval of the pressure build-up phase, the difference between the pressure (pHZ ) in the piston-cylinder system (14, HZ, THZ) and the pressure (pR1 , pR2 ) in the selected wheel brake (18a, 18b, 18c, 18d) decreases,
the solenoid valve (17a, 17b, 17c, 17d) of at least one other wheel brake (18a, 18b, 18c, 18d) being closed in at least one time interval during the displacement of the piston.
Abstract:
The method controls the electric motor piston so that braking pressure is rapidly built up in a selected wheel brake by a two-phase increase and subsequent equalization of the pressure difference between the master cylinder and the wheel brake, while solenoid valves of the remaining wheels remain closed during this pressure build-up in order to adjust the pressure quickly, precisely and energy-efficiently in a wheel-selective manner.
Technical Relevance:
The extended process turns the main piston itself into a fast "pressure pump" for one to three individual wheels, while the valves of the other wheels close during this pressure build-up; the pressure in the target brake(s) thus increases in two precisely controlled phases (first increasing the difference, then equalizing it) within a few milliseconds, without increasing or decreasing the pressure already present at the other wheels. At the end of the second phase, pressure equalization takes place between the master brake cylinder and the wheel brake cylinder. The pressure sensor in the pressure supply (piston cylinder system) then also indicates the pressure in the wheel brake cylinder. This allows the volume-pressure curve of the wheel brake cylinder to be adapted after each completed pressure change. In addition, the required target position change of the piston-cylinder system for the final target pressure to be set in the selected wheel brake(s) is calculated by knowing the volume-pressure curve of the individual wheel brakes. The process enables precise control of the brake pressures at the individual wheels without the need for expensive wheel pressure sensors. Instead, a central pressure sensor is sufficient, which ideally records the output pressure of the electric motor-driven pressure generation unit directly.
This allows wheel-selective ABS/ESC interventions, AEB maneuvers and torque vectoring to be implemented very energy-efficiently and precisely, without an additional pump unit or return flow accumulator - a significant advantage in terms of installation space, weight and cost, which is particularly relevant for electric vehicles and software-defined braking strategies (blending).
Patent E102DE2 (DE 102009061892)
CLAIM 8
Keyword: Plunger Flow Control with Pressure Curve Control
Method for adjusting a brake pressure in a brake system with four wheel brakes (18a, 18b, 18c, 18d) using a piston-cylinder system (14, HZ, THZ),
wherein a solenoid valve (17a, 17b, 17c, 17d) is associated with each of the wheel brakes (18a, 18b, 18c, 18d), the method comprising the following steps:
performing a pressure reduction in at least one selected wheel brake (18a, 18b, 18c, 18d) when a pressure change in the selected wheel brake (18a, 18b, 18c, 18d) is required,
wherein the pressure reduction in the selected wheel brake (18a, 18b, 18c, 18d) comprises the following steps:
displacement of a piston of the piston-cylinder system (14, HZ, THZ) by the electric motor, so that in a pressure reduction phase a pressure (pR1, pR2 ) is reduced at least in the selected wheel brake (18a, 18b, 18c, 18d) in such a way,
that in a first time interval of the pressure reduction phase, a difference between the pressure (pHZ ) in the piston-cylinder system (14, HZ, THZ) and the pressure (pR1, pR2 ) in the selected wheel brake (18a, 18b, 18c, 18d) increases
and in a second time interval of the pressure reduction phase, the difference between the pressure (pHZ ) in the piston-cylinder system (14, HZ, THZ) and the pressure (pR1, pR2 ) in the selected wheel brake (18a, 18b, 18c, 18d) decreases.
Claim Features
Abstract:
The method uses the motor-adjusted master cylinder piston to reduce the brake pressure in a selected wheel brake in two phases - first by increasing, then by reducing the pressure difference between master cylinder pressure (pMC) and wheel brake pressure (pWC) - in a wheel-selective manner, quickly and without disturbing the other wheels.
Technical Relevance:
The two-phase strategy turns the master piston into an active "suction pump" so that the brake pressure in a single wheel can be reduced in milliseconds and without a return accumulator. At the end of the second time interval, pressure equalization takes place between the brake master cylinder and the brake wheel cylinder. The pressure sensor in the pressure supply (piston cylinder system) then also indicates the pressure in the brake wheel cylinder. This allows the volume-pressure curve of the brake wheel cylinder to be adapted after each completed pressure change. In addition, the required target position change of the piston-cylinder system for the final target pressure to be set in the selected wheel brake(s) is calculated by knowing the volume-pressure curve of the individual wheel brakes. This process also enables precise control of the wheel pressures without the use of expensive wheel pressure sensors. As a result, wheel-selective ABS, ESC and torque vectoring interventions can be implemented particularly quickly, energy-efficiently and in a space-saving manner - a key advantage not only for software-defined braking functions in modern electric vehicles. In the area of low wheel pressures (e.g. on icy roads), the negative pressure and the large cross-sections of the valves support even faster pressure reduction in the wheels with a tendency to lock, especially compared to systems with low-pressure accumulators. This significantly improves the vehicle's stability characteristics on these safety-critical roads.
Patent E102DE2 (DE 102009061892)
CLAIM 35
Keyword: Plunger Flow Control with Pressure Curve Control
Claim Features
Method for adjusting a brake pressure in at least one wheel brake (18a, 18b, 18c, 18d) using a piston-cylinder system (14, HZ, THZ),
wherein a solenoid valve (17a, 17b, 17c, 17d) is associated with the wheel brake (18a, 18b, 18c, 18d), the method comprising the following steps:
performing a pressure build-up in the wheel brake (18a, 18b, 18c, 18d) when a pressure change in the wheel brake (18a, 18b, 18c, 18d) is required,
wherein the pressure build-up is carried out in such a way that a volume flow from the piston-cylinder system (14, HZ, THZ) through the solenoid valve (17a, 17b, 17c, 17d) into the wheel brake (18a, 18b, 18c, 18d) causes the pressure change (completely);
and performing a pressure reduction in the wheel brake (18a, 18b, 18c, 18d) when a pressure change in the wheel brake (18a, 18b, 18c, 18d) is required,
wherein the pressure reduction is carried out in such a way that a volume flow from the wheel brake (18a, 18b, 18c, 18d) through the solenoid valve (17a, 17b, 17c, 17d) into the piston-cylinder system (14, HZ, THZ) causes the pressure change (completely).
Abstract:
The method regulates brake pressure changes in a single wheel brake solely by bidirectional volume flow between the motor-driven cylinder and the wheel cylinder via its solenoid valve: for pressure build-up, fluid is shifted from the piston-cylinder system into the wheel cylinder, and for pressure reduction, volume is shifted from the wheel cylinder into the working chamber of the motor-driven piston-cylinder system through the same valve by means of selective adjustment of a pressure difference between the wheel brake and the working chamber in the piston-cylinder system. With volume flow control, the piston speed is also controlled in addition to the piston position and is not influenced by valve modulation.
Technical Relevance:
The idea turns the master cylinder into a bidirectional "actuator + buffer": the brake pressure of an individual wheel is controlled exclusively by shifting brake fluid back and forth via its solenoid valve. In contrast to methods that require digitally controlled outlet valves, this keeps noise levels low, which is important for functions such as brake torque blending and torque vectoring. In extreme cases, the process even makes it possible to dispense with valves and hydraulic lines to low-pressure accumulators or brake fluid reservoirs. This reduces component and energy requirements, while wheel-selective ABS/ESC interventions can be implemented ultra-fast, compactly and cost-effectively - a clear advantage for software-defined brake architectures in modern electric and platform vehicles.
Patent E102DE2 (DE 102009061892)
CLAIM 36
Keyword: Plunger Flow Control with Pressure Curve Control
Claim Features
A method of adjusting a brake pressure in at least one wheel brake (18a, 18b, 18c, 18d) using a piston-cylinder system (14, HZ, THZ), the method comprising the following steps:
Recording a wheel-specific pressure-volume characteristic curve for the wheel brake (18a, 18b, 18c, 18d) when the vehicle is stationary, wherein the following steps are carried out:
adjusting a piston of the piston-cylinder system (14, HZ, THZ) such that, along a piston path, a pressure (pHZ ) in the piston-cylinder system (14, HZ, THZ) corresponds to a pressure (pR1 , pR2 ) in the wheel brake (18a, 18b, 18c, 18d); and
detecting the pressure (pHZ ) in the piston-cylinder system (14, HZ, THZ) as a function of a volume in the wheel brake (18a, 18b, 18c, 18d) along the piston path in order to record the pressure-volume characteristic for the wheel brake (18a, 18b, 18c, 18d);
performing a pressure build-up and/or pressure reduction in the wheel brake (18a, 18b, 18c, 18d) when a pressure change in the wheel brake (18a, 18b, 18c, 18d) is required.
Abstract:
The method first calibrates each wheel brake when the vehicle is stationary by recording a wheel-individual pressure-volume characteristic curve via a piston path of the master brake cylinder, and then uses this characteristic curve to precisely increase or decrease the brake pressure in the respective wheel brake by means of a motor-adjusted master cylinder piston.
Technical Relevance:
The characteristic curve calibration not only compensates for manufacturing, temperature and wear tolerances on a wheel-by-wheel basis, but also for the influence of air bubbles in the brake fluid, so that the brake pressure controller always knows exactly what volume (and therefore brake pressure) its piston stroke is generating without the need of additional wheel pressure sensors; this means that brake force distribution, recuperation blending and driving dynamics control remain permanently precise and reproducible - a decisive advantage for automated driving functions with high ASIL-D requirements.
Patent E102DE3 (DE 102009061893.7)
CLAIM 1
Keyword: Plunger & ValveSync for Simultaneous Pressure Modulation and Wheel-Selective PWM Valve Control
Claim Features
Brake system with a brake booster whose piston-cylinder system (14, HZ, THZ) is mechanically or hydraulically driven by an electric motor by transmission means,
wherein at least one working chamber of the piston-cylinder system (14, HZ, THZ) is connected to at least two wheel brakes (18a, 18b, 18c, 18d) via hydraulic connecting lines,
wherein the wheel brakes (18a, 18b, 18c, 18d) are each assigned a 2/2-way switching valve (17a, 17b, 17c, 17d) and the hydraulic connecting lines between the wheel brakes (18a, 18b, 18c, 18d) and the piston-cylinder system (14, HZ, THZ) can be closed either separately or jointly by means of the 2/2-way switching valves (17a, 17b, 17c, 17d),
so that a pressure (pR1 , pR2 ) can be set in the wheel brakes (18a, 18b, 18c, 18d) simultaneously or overlapping in time, the electric motor being controllable by a control device in such a way that a (main) cylinder pressure (pHZ ) is set in a pressure build-up phase,
wherein the 2/2-way switching valves (17a, 17b, 17c, 17d) can be controlled by the control device in the pressure build-up phase in such a way that at least one first 2/2-way switching valve (17a, 17b, 17c, 17d) is closed at least in a first time interval
and at least one second 2/2-way switching valve (17a, 17b, 17c, 17d) is controlled by means of pulse width modulation in such a way that the flow resistance of the second 2/2-way switching valve (17a, 17b, 17c, 17d) is increased.
Abstract:
The patent describes an electro-hydraulic brake-by-wire (BbW) brake system in which a piston-cylinder system driven by an electric motor is selectively connected to several wheel brakes via 2/2-way switching valves, whereby a wheel-specific pressure build-up is made possible by time-shifted actuation and by variable flow resistance with definite pulse width modulation of individual valves.
Technical Relevance:
The invention enables highly dynamic, wheel-selective pressure control through a combination of piston position control and pulse width modulation of the switching valves. This is particularly relevant for driving dynamics interventions, ABS/ESC functions and precise integration of recuperation, as the brake pressure per wheel can be adjusted independently and in fine doses.
Patent E102DE3 (DE 102009061893.7)
CLAIM 4
Keyword: Plunger & ValveSync for Simultaneous Pressure Modulation and Wheel-Selective PWM Valve Control
Claim Features
Brake system with a brake booster whose piston-cylinder system (14, HZ, THZ) is mechanically or hydraulically driven by an electric motor by transmission means,
at least one working chamber of the piston-cylinder system (14, HZ, THZ) being connected via hydraulic connecting lines to at least two wheel brakes (18a, 18b, 18c, 18d), the wheel brakes (18a, 18b, 18c, 18d) each being assigned a 2/2-way switching valve (17a, 17b, 17c, 17d)
and the hydraulic connecting lines between the wheel brakes (18a, 18b, 18c, 18d) and the piston-cylinder system (14, HZ, THZ) can be closed either separately or jointly by means of the 2/2-way switching valves (17a, 17b, 17c, 17d), so that a pressure (pR1, pR2 ) can be set simultaneously in the wheel brakes (18a, 18b, 18c, 18d),
wherein the electric motor can be controlled by a control device in such a way that, in a pressure reduction phase, a (main) cylinder pressure (pHZ ) generated by means of the piston-cylinder system (14, HZ, THZ) is changed over time, preferably reduced in a time interval,
so that at least in one time interval, a piston speed of the piston-cylinder system (14, HZ, THZ) varies over time, in particular increases and/or decreases,
wherein the 2/2-way switching valves (17a, 17b, 17c, 17d) can be controlled by the control device in the pressure reduction phase in such a way that at least in the time interval the pressure (pR1, pR2 ) in the wheel brakes is simultaneously reduced into the working chamber of the piston-cylinder system (14, HZ, THZ) when the 2/2-way switching valves (17a, 17b, 17c, 17d) are open.
Abstract:
The patent describes an electro-hydraulic brake-by-wire (BbW) brake system in which the piston of a brake booster driven by an electric motor selectively reduces the brake pressure in several wheel brakes via 2/2-way switching valves by varying the piston speed over time and simultaneously returning brake fluid from the opened wheel brake circuits to the pressure-generating electromechanically driven piston-cylinder system.
Technical Relevance:
The invention enables a controlled, simultaneous pressure reduction in several wheel brakes through definite control of the piston speed in the master cylinder, whereby a high-precision, wheel-wide coordinated brake pressure reduction can be realized.
This is particularly relevant for modern pressure control strategies in driving dynamics interventions and recuperation processes - such as wheel- or axle-specific regenerative braking, electric brake force distribution or torque vectoring - where rapid but sensitive pressure reduction is essential for vehicle stability and dynamic performance.
Patent E102DE3 (DE 102009061893.7)
CLAIM 5
Keyword: Plunger & ValveSync for Simultaneous Pressure Modulation and Wheel-Selective PWM Valve Control
Claim Features
Brake system with a brake booster whose piston-cylinder system (14, HZ, THZ) is mechanically or hydraulically driven by an electric motor by transmission means,
at least one working chamber of the piston-cylinder system (14, HZ, THZ) being connected via hydraulic connecting lines to at least two wheel brakes (18a, 18b, 18c, 18d), the wheel brakes (18a, 18b, 18c, 18d) each being assigned a 2/2-way switching valve (17a, 17b, 17c, 17d), 17c, 17d) is assigned to each of the wheel brakes (18a, 18b, 18c, 18d) and the hydraulic connecting lines between the wheel brakes (18a, 18b, 18c, 18d) and the piston-cylinder system (14, HZ, THZ) can be closed either separately or jointly by means of the 2/2-way switching valves (17a, 17b, 17c, 17d),
so that a pressure (pR1, pR2 ) can be set simultaneously in the wheel brakes (18a, 18b, 18c, 18d), wherein the electric motor can be controlled by a control device in such a way that in a pressure build-up phase a (main) cylinder pressure (pHZ ) generated by means of the piston-cylinder system (14, HZ, THZ) is changed over time, preferably increased in a time interval,
wherein the 2/2-way switching valves (17a, 17b, 17c, 17d) can be controlled by the control device in the pressure build-up phase such that at least in a first time interval the pressure (pR1, pR2 ) is built up simultaneously in at least a first wheel brake (18a, 18b, 18c, 18d) and a second wheel brake (18a, 18b, 18c, 18d) when the 2/2-way switching valves (17a, 17b, 17c, 17d) are open,
and that in a second time interval, which is downstream of the first time interval, the pressure (pR1, pR2 ) in at least the first wheel brake (18a, 18b, 18c, 18d) is built up simultaneously when the 2/2-way switching valve (17a, 17b, 17c, 17d) is further built up, while the pressure build-up in at least the second wheel brake (18a, 18b, 18c, 18d) is stopped by closing the 2/2-way switching valve (17a, 17b, 17c, 17d).
Abstract:
The patent describes an electro-hydraulic brake-by-wire (BbW) brake system in which the piston driven by an electric motor enables a wheel-selective pressure build-up during pressure build-up via selectively controlled 2/2-way switching valves, so that in a first time interval the pressure in several wheel brakes can be increased simultaneously, while in a subsequent time interval the pressure is selectively built up or stopped only in individual wheels.
Technical Relevance:
The invention enables a time-staggered, wheel-selective pressure build-up via selectively switched 2/2-way valves, whereby electric brake force distribution (EBD) as well as axle- or wheel-specific regenerative braking can be precisely realized. This is particularly relevant for modern vehicles with hybrid or electric drives, in which mechanical and recuperative braking torques must be distributed dynamically and efficiently, especially in combination with driving dynamics interventions.
Patent E102DE4 (DE 102009061894.5)
CLAIM 1
Keyword: Plunger Volume Flow Estimation based on modeling of hydraulic layout
Claim Features
Method for adjusting a brake pressure in a brake system with at least two wheel brakes (18a, 18b, 18c, 18d) using a piston-cylinder system (14, HZ, THZ), each of the wheel brakes (18a, 18b, 18c, 18d) being assigned a respective solenoid valve (17a, 17b, 17c, 17d), the method comprising the following steps
carrying out a pressure build-up in at least a first wheel brake (18a, 18b, 18c, 18d) and a second wheel brake (18a, 18b, 18c, 18d) when a pressure change, in particular a pressure increase, is required in the first and second wheel brakes (18a, 18b, 18c, 18d),
wherein the following steps are carried out during the pressure build-up:
Adjusting a piston of the piston-cylinder system (14, HZ, THZ) so that a pressure is built up in the wheel brakes (18a, 18b, 18c, 18d) simultaneously or overlapping in time;
determining an actual pressure (pHZ ) in the piston-cylinder system (14, HZ, THZ) as an input variable for a pressure model;
determining a first actual pressure (pR1 , pR2 ) in the first wheel brake (18a, 18b, 18c, 18d) and a second actual pressure (pR1 , pR2 ) in the second wheel brake (18a, 18b, 18c, 18d) by means of the pressure model and using the actual pressure (pHZ ) in the piston-cylinder system (14, HZ, THZ); and
closing the solenoid valve (17a, 17b, 17c, 17d) of the first wheel brake (18a, 18b, 18c, 18d) when the first actual pressure (pR1 , pR2 ) corresponds to a target pressure of the first wheel brake (18a, 18b, 18c, 18d).
Abstract:
The patent describes a method for wheel-selective pressure build-up in an electro-hydraulic brake-by-wire (BbW) brake system, in which the piston of a piston-cylinder system builds up pressure in several wheel brakes simultaneously or overlapping in time, whereby the individual wheel brake pressures are calculated by means of a pressure model and measured master cylinder pressure and the associated solenoid valves are closed in a definite manner as soon as the respective target pressure is reached.
Technical Relevance:
The invention enables model-based, high-precision control of the brake pressure at each individual wheel without the need for additional wheel brake pressure sensors.
It is particularly relevant for electric brake force distribution and wheel-specific regenerative braking, as the valves are automatically closed as soon as the calculated pressure value reaches the specified target pressure - a key component for efficient, adaptive and safe braking strategies in modern vehicle architectures.
Patent E102DE4 (DE 102009061894.5)
CLAIM 2
Keywords: Plunger Volume Flow Estimation based on modeling of hydraulic layout
Claim Features
A method of adjusting a brake pressure in a brake system having at least two wheel brakes (18a, 18b, 18c, 18d) using a piston-cylinder system (14, HZ, THZ),
wherein a solenoid valve (17a, 17b, 17c, 17d) is associated with each of the wheel brakes (18a, 18b, 18c, 18d), the method comprising the following steps:
carrying out a pressure build-up in at least a first wheel brake (18a, 18b, 18c, 18d) and a second wheel brake (18a, 18b, 18c, 18d) when a pressure change, in particular a pressure increase, is required in the first and second wheel brakes (18a, 18b, 18c, 18d),
wherein the following steps are carried out during the pressure build-up: Adjusting a piston of the piston-cylinder system (14, HZ, THZ) so that a pressure is built up in the wheel brakes (18a, 18b, 18c, 18d)
simultaneously or overlapping in time;
Determining the actual position of the piston as an input variable for a pressure model;
determining a first actual pressure (pR1, pR2 ) in the first wheel brake (18a, 18b, 18c, 18d) and a second actual pressure (pR1, pR2 ) in the second wheel brake (18a, 18b, 18c, 18d) by means of the pressure model and using the actual position of the piston; and
closing the solenoid valve (17a, 17b, 17c, 17d) when the first actual pressure (pR1, pR2 ) corresponds to a target pressure of the first wheel brake (18a, 18b, 18c, 18d).
Abstract:
The patent describes a method for wheel-selective brake pressure build-up, in which pressure is built up in several wheel brakes simultaneously or with a time delay by adjusting a piston, whereby the current brake pressure in the wheel brake cylinder is determined on the basis of the piston position and the associated solenoid valve which is automatically closed as soon as the desired target pressure is reached.
Technical Relevance:
The innovation enables sensorless, model-based pressure control in each individual wheel brake cylinder, solely by evaluating the piston position, without the need for separate pressure sensors on the wheel brakes. This is particularly relevant for recuperative braking systems and electric brake force distribution, as the solution is cost-efficient, precise and ideal for quickly controllable, wheel-specific interventions in modern brake-by-wire architectures.
Patent E102DE4 (DE 102009061894.5)
CLAIM 3
Keyword: Plunger Volume Flow Estimation based on modeling of hydraulic layout
Claim Features
A method of adjusting a brake pressure in a brake system having at least two wheel brakes (18a, 18b, 18c, 18d) using a piston-cylinder system (14, HZ, THZ),
wherein a solenoid valve (17a, 17b, 17c, 17d) is associated with each of the wheel brakes (18a, 18b, 18c, 18d), the method comprising the
following steps:
carrying out a pressure build-up in at least a first wheel brake (18a, 18b, 18c, 18d) and a second wheel brake (18a, 18b, 18c, 18d) when a pressure change, in particular a pressure increase, is required in the first and second wheel brakes (18a, 18b, 18c, 18d), wherein the following steps are carried out during the pressure build-up:
Adjusting a piston of the piston-cylinder system (14, HZ, THZ) so that a pressure is built up in the wheel brakes (18a, 18b, 18c, 18d) simultaneously or overlapping in time;
determining an actual pressure (pHZ ) in the piston-cylinder system (14, HZ, THZ) as an input variable for a pressure model and/or determining an actual position of the piston as an input variable for a pressure model; and
determining a first actual pressure (pR1 , pR2 ) in the first wheel brake (18a, 18b, 18c, 18d) and a second actual pressure (pR1 , pR2 ) in the second wheel brake (18a, 18b, 18c, 18d) by means of the pressure model and using the actual pressure (pHZ ) in the piston-cylinder system (14, HZ, THZ) and/or using the actual position of the piston.
Abstract:
The patent describes a method for model-based, wheel-selective brake pressure build-up in an electro-hydraulic brake-by-wire (BbW) brake system, in which pressure is built up in several wheel brakes simultaneously or overlapping in time via the adjustment of a piston and the respective wheel brake pressure is calculated on the basis of the measured master cylinder pressure and/or the piston position using a pressure model - without the use of wheel pressure sensors.
Technical Relevance:
The invention enables high-precision, sensorless pressure control per wheel by using a flexible pressure model based either on the master cylinder pressure, the piston position or a combination of both. This is particularly relevant for adaptive braking systems with electric brake force distribution, torque vectoring or wheel-selective recuperation, as it allows finely dosed, energy-efficient and cost-optimized pressure control in brake-by-wire systems.
Patent E102DE4 (DE 102009061894.5)
CLAIM 4
Keyword: Plunger Volume Flow Estimation based on modeling of hydraulic layout
Claim Features
A method of adjusting a brake pressure in a brake system having at least two wheel brakes (18a, 18b, 18c, 18d) using a piston-cylinder system (14, HZ, THZ),
wherein a solenoid valve (17a, 17b, 17c, 17d) is associated with each of the wheel brakes (18a, 18b, 18c, 18d), the method comprising the
following steps:
carrying out a pressure reduction in at least a first wheel brake (18a, 18b, 18c, 18d) and a second wheel brake (18a, 18b, 18c, 18d) when a pressure change, in particular a pressure reduction, is required in the first and second wheel brakes (18a, 18b, 18c, 18d),
wherein the following steps are carried out during the pressure reduction:
Adjusting a piston of the piston-cylinder system (14, HZ, THZ) so that a pressure is reduced in the wheel brakes (18a, 18b, 18c, 18d) simultaneously or overlapping in time;
determining an actual pressure (pHZ ) in the piston-cylinder system (14, HZ, THZ) as an input variable for a pressure model and/or determining an actual position of the piston as an input variable for a pressure model; and
determining a first actual pressure (pR1 , pR2 ) in the first wheel brake (18a, 18b, 18c, 18d) and a second actual pressure (pR1 , pR2 ) in the second wheel brake (18a, 18b, 18c, 18d) by means of a pressure model and using the actual pressure (pHZ ) in the piston-cylinder system (14, HZ, THZ) and/or using the actual position of the piston.
Abstract:
The patent describes a method for model-based, wheel-selective pressure reduction in an electro-hydraulic brake-by-wire (BbW) brake system, in which the brake pressure in several wheel brakes is reduced simultaneously or overlapping in time by adjusting a piston, the actual wheel brake pressures being determined on the basis of the pressure measured in working chamber of electromotive piston and/or the piston position using a model.
Technical Relevance:
The innovation enables precise pressure reduction per wheel without the need of wheel pressure sensors - central for safety functions such as ABS, ESC or AEB, but also for recuperative braking strategies with active torque shifting. The model-based evaluation of piston position and/or master cylinder pressure means that expensive wheel brake pressure sensors can be dispensed with, while at the same time fast, wheel-selective and sensitive pressure reduction is guaranteed.
Patent E102DE4 (DE 102009061894.5)
CLAIM 5
Keyword: Plunger Volume Flow Estimation based on modeling of hydraulic layout
Method for adjusting a brake pressure in a brake system with at least two wheel brakes (18a, 18b, 18c, 18d) using a piston-cylinder system (14,A method of adjusting a brake pressure in a brake system having at least two wheel brakes (18a, 18b, 18c, 18d) using a piston-cylinder system (14, HZ, THZ), wherein each of the wheel brakes (18a, 18b, 18c, 18d) is associated with a respective solenoid valve (17a, 17b, 17c, 17d), the method comprising the following steps:
performing a pressure build-up in at least a first wheel brake (18a, 18b, 18c, 18d) and a second wheel brake (18a, 18b, 18c, 18d) using the steps of the pressure build-up according to claim 3 in a first time interval when a pressure change, in particular a pressure increase, is required in the first and second wheel brakes (18a, 18b, 18c, 18d);
and performing a pressure reduction in at least the first wheel brake (18a, 18b, 18c, 18d) and the second wheel brake (18a, 18b, 18c, 18d) using the steps of the pressure reduction according to claim 4 in a second time interval when a pressure change, in particular a pressure reduction, is required in the first and second wheel brakes (18a, 18b, 18c, 18d),
the second time interval following the first time interval in time.
Claim Features
Abstract:
The patent describes a method for wheel-selective brake pressure build-up or reduction, in which pressure is initially built up in a model-based manner in several wheel brakes via a piston-cylinder system in a first time interval and then reduced again in a model-based manner in a second, time-delayed interval - in each case by means of definite valve control and using piston position and/or master cylinder pressure as control variables.
Technical Relevance:
The invention allows continuous, model-based control of the brake pressure over the entire braking process - from initial pressure build-up to targeted pressure reduction - without the use of wheel brake pressure sensors.
This is particularly relevant for recuperative braking systems, electric brake force distribution and driving dynamics functions, where pressure must be adjusted precisely, in time and wheel-selectively in order to optimally combine energy efficiency, safety and driving stability.