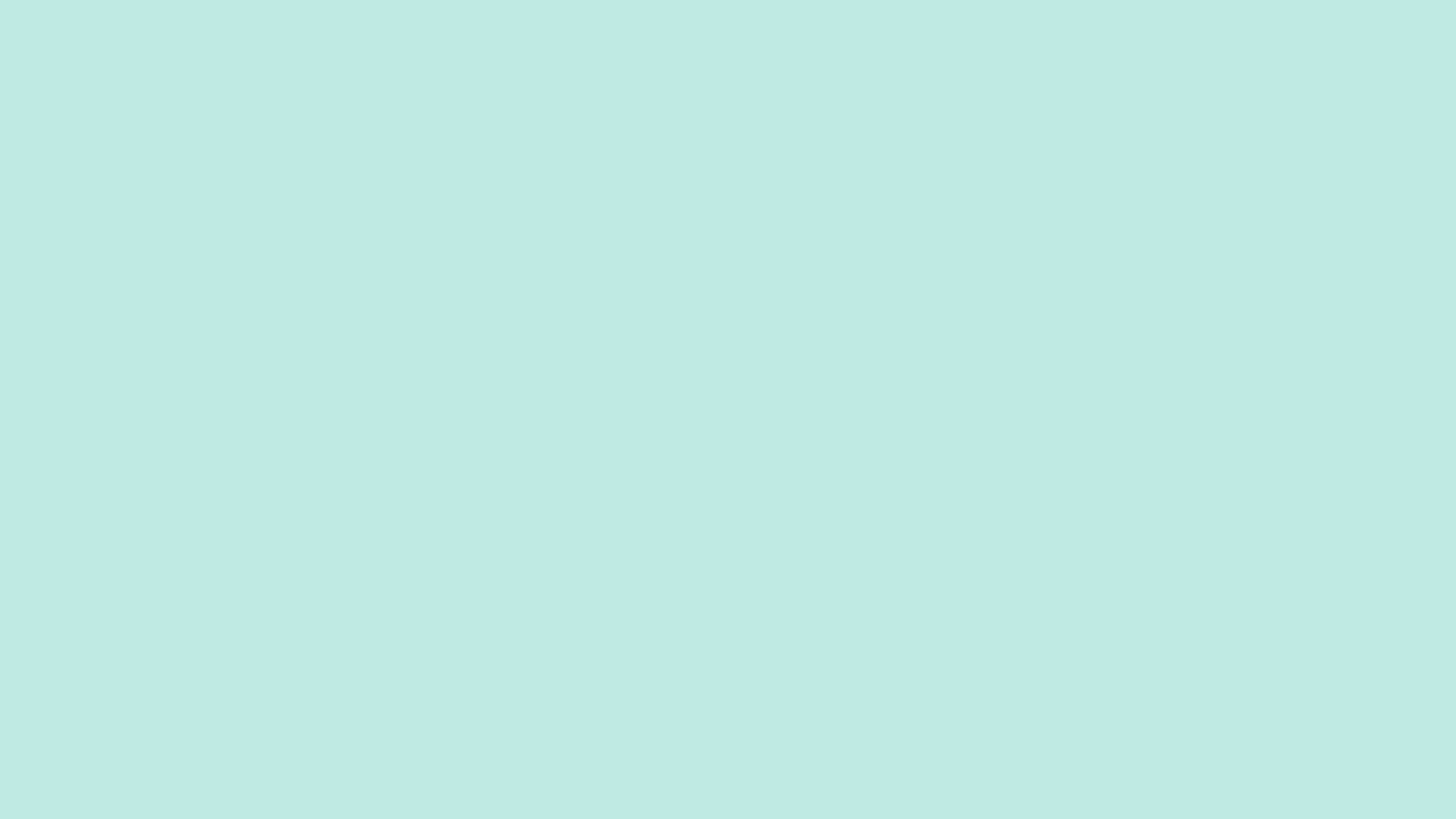
E132
15.2.2012
Patent E32 - IP Portfolio A2
Plunger-Based Brake-by-Wire Architecture
Inventor: H. Leiber
5 Core Innovations
Patent E132DE1
Safe Actuator - Modular Brake Control Unit with Redundant Circuits and Integrated Valve Diagnostics
Plunger-3CH - with Switchable Reservoir and Circuit Separation
Two Claims
Patent Status : Examinig
Patent E132DE
Single-Circuit Plunger with saferty valves for brake circuit selection and central pressure sensing
One Claim
Patent Status : Granted
Patent E132DE2
Plunger Diag - Active brake circuit fault detection via closed-system pressure modulation
One Claim
Patent Status : Granted
Patent E132DE3
Plunger Multi function - Multi functional plunger with highly dynamic pressure control (HPC)
One Claim
Patent Status: Granted
Patent E132DE-SA (DE 102012002791)
CLAIM 1
Keywords: Single-circuit Plunger with Separation Valves for Brake Circuit Selection
Brake actuating device, having an actuating device, a travel simulator (21), a first piston-cylinder device (3) having a first piston (2) and a further piston (4),
wherein the first (2) and the further piston (4) each form a working chamber, wherein first hydraulic connections (11, 12) lead from the working chambers of the first piston-cylinder device (3) to wheel brakes, wherein first valve devices are provided in the first hydraulic connections (11, 12), and with a booster device (25) driven by an electric motor, which has a second piston-cylinder device (26) with exactly one working chamber, which is connected to the wheel brake via a second hydraulic connection, in which a second valve device is provided, and is connected to a reservoir (7) via a third hydraulic connection, in which a third valve device is provided,
wherein the booster device (25), which is driven by an electric motor, actuates a plunger piston (29),
characterized in that the first valve devices have an on-off switching valve (15, 16, 17, 18) for each wheel brake,
wherein safety valves (33, 34) are arranged in the hydraulic lines from the second piston-cylinder device (26) to the wheel brakes,
wherein a pressure sensor (38) is arranged between the working chamber (30) of the second piston-cylinder device (26) and the safety valves (33, 34),
wherein the first piston (2) actuated by the actuating device is used to control the displacement simulator (21).
Feature Claims
Abstract:
The invention relates to an electro-hydraulic brake-by-wire actuation unit in which the mechanically actuated master cylinder is not used to generate pressure directly, but is used in connection with a pedal feel simulator. The actual brake pressure is generated by an electric motor-driven booster unit with a plunger , which is connected to the wheel brakes and the reservoir via separate valve paths. The pressure is supplied by means of individually controllable inlet/outlet switching valves for each wheel brake as well as safety valves and a pressure sensor for monitoring and controlling the hydraulic pressure between the plunger and wheel circuits.
Technical Relevance:
The invention describes a minimalist but functionally highly effective brake-by-wire architecture with a single-circuit plunger that has exactly one hydraulic working chamber. This working chamber is connected to two separate brake circuits via a safety valve, thus achieving a high degree of system safety despite the single-circuit configuration. The pressure is controlled exclusively using a centrally positioned pressure sensor between the plunger and the safety valves - which reduces the sensor effort, minimizes system complexity and still enables precise brake pressure modulation in the closed brake circuit (reference to E102 patent family). This control is based on software-supported pressure models that continuously compare the plunger pressure with the expected wheel brake pressures.
This architecture has become established in modern electro-hydraulic one-box brake-by-wire systems and is used in particular for driver assistance functions (Automatic Cruise Control ACC, Automatic Emergency Braking AEB), regenerative braking and can be used to improve ABS operation at low friction values (low-µ).
Patent E132DE1 (DE 102012025960)
CLAIM 1
Keywords: Modular Brake Control Unit with Redundant Circuits and Integrated Valve Diagnostics
Brake actuating device, with an actuating device, in particular a brake pedal (1),
a travel simulator (21),
a first and a second brake circuit, each with two wheel brakes (15-18),
a first piston-cylinder device (3) with a first piston (2) and a second piston (4), which each delimit a first working chamber (5) and a second working chamber (6), wherein the working chambers (5, 6) are each separably connected to one of the brake circuits via hydraulic connections (11, 12), and
a booster device (25) driven by an electric motor, which has a second piston-cylinder device (26) for building up and/or reducing a pressure in a common hydraulic connecting line,
wherein the common hydraulic connection line is connected to the first brake circuit via a first safety valve (33) and to the second brake circuit via a second safety valve (34);
characterized in that the brake actuating device is designed to implement ABS and traction control and/or assistance functions using the second piston-cylinder unit,
wherein a pressure control with variable pressure rise and, in particular, pressure drop rates takes place
and the brake circuits pressurized by the second piston-cylinder unit (26) can be separated by means of the safety valves,
wherein the brake actuating device implements a diagnostic function for determining the switching function and/or the tightness of some, preferably all, solenoid valves.
Feature Claims
Abstract:
The brake actuation device combines a brake pedal with pedal feel simulator, two hydraulically separable brake circuits, an electromotive booster unit with separate piston-cylinder unit for pressure control (incl. ABS/ASR/assistance functions), separable safety valves and an integrated diagnostic function for solenoid valves.
Technical Relevance:
The focus of the diagnostics is on checking the tightness and functionality of the safety valves to the electric motor-driven plunger as well as the tightness of the isolating valves, which are closed when energized during normal operation and isolate the master cylinder from the system. This is crucial to ensure that the brake master cylinder is reliably hydraulically decoupled in brake-by-wire mode and that, in the event of an electrical power or motor failure of the plunger - in the so-called fall-back level - no brake fluid volume unintentionally enters the working chamber of the plunger when the brake pedal is pressed and pressure builds up and pushes the plunger back.
In addition, the invention makes it possible to diagnose the wheel switching valves to detect a wheel circuit failure - provided that these are not equipped with check valves connected in parallel. In one-box brake systems currently used as standard, check valves are used for safety reasons. However, these check valves prevent precise diagnosis, as in the event of a fault it is not possible to clearly determine whether a leak is caused by the switching valve or the check valve path. For this reason, an entire brake circuit with two wheel brakes must always be switched off in the event of fault symptoms.
The diagnostic function integrated in this invention makes a significant contribution to the operational safety of modern brake-by-wire systems.
Patent E132DE1 (DE 102012025960)
CLAIM 2
Keywords: Plunger-3 CH with Switchable Reservoir and Circuit Separation
Brake actuating device, with an actuating device, in particular a brake pedal (1),
a travel simulator (21),
a first and a second brake circuit, each with two wheel brakes (15-18),
a first piston-cylinder device (3) with a first piston (2) and a second piston (4), which each delimit a first working chamber (5) and a second working chamber (6), wherein the working chambers (5, 6) are each separably connected to one of the brake circuits via hydraulic connections (11, 12), and
a booster device (25) driven by an electric motor, which has a second piston-cylinder device (26) for building up and/or reducing a pressure in a common hydraulic connecting line,
wherein the common hydraulic connection line is connected to the first brake circuit via a first safety valve (33) and to the second brake circuit via a second safety valve (34);
characterized in that the brake actuating device is designed to implement ABS and traction control and/or assistance functions using the second piston-cylinder unit,
wherein a pressure control with variable pressure rise and, in particular, pressure drop rates takes place
and the brake circuits pressurized by the second piston-cylinder unit (26) can be separated by means of the safety valves,
wherein the second piston-cylinder device (26) comprises a plunger working chamber which is connected to a reservoir (7) via a third valve device, namely a switching valve.
Feature Claims
Abstract:
The brake actuating device combines a brake pedal with travel simulator, two brake circuits which can be hydraulically separated via safety valves and an electromotor-controlled booster unit with variable pressure control, wherein an integrated switching valve connects the plunger working chamber of the second piston-cylinder unit specifically to the reservoir - for implementing further diagnostics and the residual friction torque control of the brake linings by generating negative pressure in the plunger working chamber.
Technical Relevance:
The described plunger circuit enables active brake line clearance control in accordance with the basic principles of the ipgate patent family E114 (EP 2225133). A vacuum of 0.5 to 0.7 bar is generated by targeted return movement of the piston to the reservoir when the valve is closed, which can be used to increase the clearance gap between the pad and brake disk in a controlled manner
In combination with safety valves and model-based pressure modulation via a plunger with a central pressure sensor, this invention represents an energy-efficient, diagnosable and safety-relevant extension of modern brake-by-wire systems - particularly with regard to the reduction of residual friction torques in wheel brakes (so-called low-drag/zero-drag brakes) in electric vehicles. This is particularly advantageous in phases following a displacement of the brake caliper pistons by the actuator of the electric parking brake, as the brake caliper pistons cannot be reset by the effect of the so-called rollback rings as is usually the case. The resetting effect is inadequate without hydraulically pressing the rollback rings into their specially shaped sealing groove. This is why the vacuum reset can score points here.
Patent E132DE2 (DE 102012025961)
CLAIM 1
Keywords: Plunger-Diag - Active Brake Circuit Fault Detection via Closed-System Pressure Modulation
Brake system for diagnosing failures and/or leaks with an electric motor-driven piston-cylinder unit (26),
wherein a safety valve (33, 34) is arranged between a first brake circuit and the piston-cylinder unit and between a second brake circuit and the piston-cylinder unit,
in order to isolate the respective brake circuit from the second piston-cylinder unit in the event of a brake circuit failure,
wherein the brake system is designed to detect a failure of at least one brake circuit by pressure modulation in the closed brake circuit,
wherein the electromotively driven piston-cylinder device (26) is designed to achieve the pressure modulation by driving a plunger piston (29) of the piston-cylinder device (26).
Feature Claims
Abstract:
The brake system detects leaks or failures of a brake circuit by specific pressure modulation in the closed system by means of a plunger piston of a piston-cylinder unit actuated by an electric motor, wherein safety valves enable the separation of faulty brake circuits from the piston-cylinder unit.
Technical Relevance:
The technical relevance of this innovation is high - it addresses a central safety problem of modern brake-by-wire and one-box brake systems, namely the early, active and redundancy-capable diagnosis of brake circuit failures and leaks without having to rely on conventional haptic feedback or external pressure sensors.
The focus of the diagnostics is on checking the tightness and functionality of the safety valves to the electric motor-driven plunger as well as the tightness of the isolating valves, which are closed when energized during normal operation and separate the brake master cylinder from the brake circuits. This is crucial to ensure that the brake master cylinder is reliably hydraulically decoupled in brake-by-wire mode and that, in the event of a electrical power or motor failure of the plunger - in the so-called fall-back level - no brake fluid volume unintentionally enters the working chamber of the plunger when the brake pedal is pressed and pressure builds up and pushes the plunger back.
In addition, the invention makes it possible to diagnose the wheel switching valves to detect a wheel circuit failure - provided that these are not equipped with check valves connected in parallel. In one-box brake systems currently used as standard, check valves are used for safety reasons. However, these check valves prevent precise diagnosis of each wheel circuit, as in the event of a fault it cannot be clearly determined whether a leak is caused by the switching valve or by the check valve path. For this reason, a brake circuit with two wheel brakes must always be switched off in the event of fault symptoms in 1-box brake systems. The architecture with wheel brakes iwith inlet and outlet valves but inlet valves without check valves connected in parallel has therefore been pursued further in more recent innovations from ipgate AG.
Patent E132DE3 (DE 102012025970)
CLAIM 1
Keywords: Plunger-Multi function- Multi-functional plunger with highly dynamic pressure control (HDC)
Brake actuating device, comprising an actuating device, in particular a brake pedal (1);
a travel simulator (21);
a first and a second brake circuit with two wheel brakes each;
a first piston-cylinder device (3) with a first piston (2) and a second piston (4), each of which delimits a first working chamber and a second working chamber, wherein the working chambers are each separably connected to one of the brake circuits via hydraulic connections (11, 12); and a booster device (25) driven by an electric motor, which has a second piston-cylinder device (26) for building up and/or reducing a pressure in a common hydraulic connecting line,
wherein the common hydraulic connection line is connected to the first brake circuit via a first safety valve (33) and to the second brake circuit via a second safety valve (34),
characterized in that the brake actuating device is designed to implement ABS and traction control and/or assistance functions using the second piston-cylinder device (26),
wherein the brake circuits pressurized by the second piston-cylinder device (26) can be separated by means of the safety valves (33, 34),
wherein a pressure sensor (38) is arranged between a working chamber (30) of the second piston-cylinder device (26) and the safety valves (33, 34).
Feature Claims
Abstract:
The brake actuating device combines a pedal-operated system with an electromotive booster unit which pressure-regulates or pressure-controls ABS, traction slip and assistance functions by pressure build-up or reduction by forward and backward movement of a plunger piston, whereby a circuit separation is performed via two safety valves.
Technical Relevance:
Brake-by-wire core architecture for implementing ABS control and dynamic driving assistance functions.
While commercially available one-box EHB systems in ABS operation at high friction values (so-called high-µ, e.g. dry road surface) traditionally reduce the pressure directly into the reservoir via outlet valves, the present invention offers a supplementary control strategy: at low friction values (e.g. snow or ice - low-µ), the pressure can alternatively be reduced via the plunger. This brings considerable advantages for volume management during longer ABS braking operations with high volume displacements and at the same time helps to reduce noise development.
A major problem with conventional systems is that the plunger reaches its volume limit due to repeated pressure reduction in the reservoir, which means that the ABS control process typically has to be interrupted for around 150 ms in order to replenish volume from the reservoir. This interruption can not only lead to longer braking distances, but can also impair driving stability. The invention offers an effective solution here by means of an adaptive control strategy, in which the pressure is reduced depending on the driving situation either via the outlet valves (prior art), but also specifically via the plunger in certain situations, e.g. long braking on snow and ice. An advantageous hybrid strategy of the two pressure control methods enables continuous, responsive and stability-enhancing ABS control even under difficult road conditions - without safety-critical interruptions.
In contrast to ABS operation using outlet valves, pressure control for other centralized driving functions - in particular for adaptive cruise control (ACC) or automated emergency braking (AEB) with extremely fast pressure build-up as well as regenerative braking – takes place in a closed brake circuit, i.e. pressure build-up and pressure reduction via plungers. In these cases, the brake pressure is modulated highly dynamically via piston path pressure control in combination with bidirectionally acting valves, which enables precise, sensitive and at the same time energy-efficient brake control in accordance with the teachings of the E102 family.